

The Massachusetts Institute of Technology University and Beijing Institute of Technology University have pointed out that natural frequency, shock pulse width, acceleration amplitude, etc. To better analyze the shock resistance of the gyroscope and guide the design of the support and protection structure, it is necessary to model and analyze the impact response characteristics of the gyroscope. The failure modes of the mechanical structure after the shock mainly include comb tooth fracture, beam and structure fracture, and particle pollution. The School of Electrical Engineering of Aalto University in Finland has conducted a shock test on a three-axis gyroscope. In the actual application environment, the device may withstand great mechanical impact for example, when the device falls from a height of 1.5 m onto concrete ground, the shock acceleration is about 500~3500 g.

Unlike mechanical vibration stress, its acceleration amplitude is very high, the shock pulse width is small, and the shock waveform is like a half-sine wave or square wave pulse. Shock is one of the most important factors affecting the reliability of MEMS. Sometimes, the gyroscope will operate in a very abominable environment, such as a high-shock environment. With the continuous research and development of MEMS quartz tuning forks resonant gyroscopes, the application field of this gyroscope is becoming wider, and the application environment is also harsher and more complex. The MEMS quartz tuning forks resonant gyroscopes from these companies account for more than 90% of the military and civilian markets. The gyroscope’s shock resistance is verified through shock testing.Īt present, there are many companies in the world researching MEMS quartz tuning forks resonant gyroscopes and putting them into the market, including Microcomponents SA, Watson Industries, Toyota BEI Systron Donner, etc. After the modal analysis and shock simulation (the half-cycle sine shock pulse with amplitude of 1500 g (g is the acceleration of gravity) and duration of 2 ms in the six shock directions), the results show that when the beam thickness is 80 μm, the maximum stress is 94.721 MPa, which is less than the failure stress of quartz crystal. In this article, the MEMS quartz tuning forks gyroscope with different V-shaped beam thicknesses are simulated and analyzed by finite element analysis simulation software. This structure determines the natural frequency of the gyroscope, and more importantly, determines the shock resistance of the gyroscope structure. The elastic structure (V-shaped beam) between the anchor support point and tuning forks plays a vital role in the MEMS quartz tuning forks resonant gyroscope.
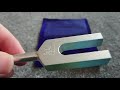
The Micro Electronics Mechanical System(MEMS) quartz tuning forks resonant gyroscope is one of the quartz gyroscopes. As a high-quality material for manufacturing gyroscopes, quartz crystals need to be designed and optimized to meet the normal operation of gyroscopes in harsh environments. The application of gyroscopes in harsh environments has always been a hot topic.
